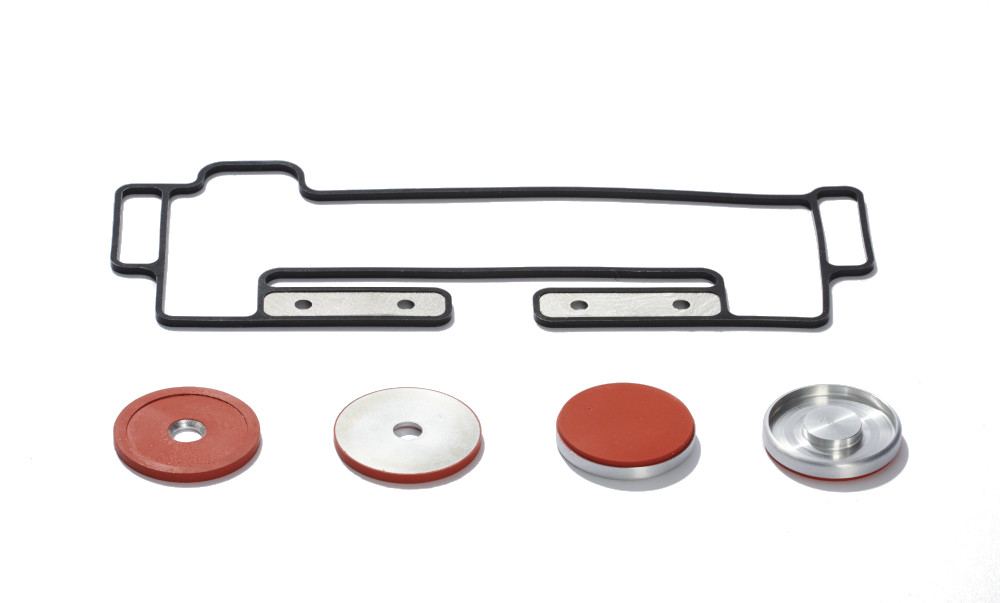
Stockwell Elastomerics provides high performance compression molded and liquid injection molded silicone products. For specialty applications, Stockwell Elastomerics also provides insert molded silicone and fluorosilicone parts. During insert molding, a component that was previously molded, formed, stamped, laser cut, or machined is preloaded into a mold. The silicone compound is then molded over and around the part. The silicone adheres to preloaded component either through mechanical or adhesive functionality.
Insert molding combines the advantages of silicone rubber with the benefits of using another material. For example, a softer and more compressible silicone can be used with a harder and more impact-resistant metal or plastic component. Insert molded components can also eliminate secondary operations and streamline downstream assembly reducing total production time and cost.
Below are some technical elements to consider when designing parts. Stockwell Elastomerics can provide holistic design for manufacturing feedback for insert molding, as well as provide pros and cons along with alternative options to meet project needs. Stockwell Elastomerics recognizes that the gasket is often the last component specified in a design, and works as an extension of customers’ teams through the design process, particularly when there is urgency.
Insert Molding vs. Co-molding for Overmolded Parts
Unlike co-molding, a process in which two different parts are molded together at the same time, insert molding involves two separate cycles. Yet the term “overmolded part” may be used for both types of molding processes. With insert molding, the overmolded part is an existing component over which the silicone rubber is molded. During overmolding, the overmolded part is produced at the same time as the silicone overmold and is fully or partially covered by the overmold.
Silicone Has Low Surface Energy. How is Insert Molding Silicone Done?
Its low surface energy is one of the properties that makes silicone a great gasketing choice and means that very few things stick to it, making silicone less susceptible to degradation and chemical attack. That property can make it a challenge for manufacturing processes like insert molding.
There are multiple ways to overcome this challenge, each with some pros and cons. Mechanical “bonding” is the most common. This requires the mold design to incorporate undercuts into the part such that silicone is molded through and/or around the insert. The tear resistance of the silicone becomes the strength limiting factor.
- Pros: The process is repeatable and predictable compared to other attachment methods.
- Cons: Geometry limitations – undercuts can reduce silicone material performance – undercut distance will determine “bonding”, and a shorter distance will reduce bond strength.
Other methods include surface preparation of the component being overmolded or additives in the molding compound. The additive or surface preparation substance is determined by the material composition of the insert component and the molding compound.
- Pros: More flexibility for smaller parts and parts with complicated geometries – simplified mold design translates to lower cost for tooling and a more robust molding process.
- Cons: Processing challenges associated with surface treatment and additive chemicals – chemistry requires precision, and if it’s inconsistent, it can lead to poor adhesive and lower repeatability.
Insert Molding for Stiffening and Ruggedization
Insert molding can be used in customer applications to limit deflection, promote stiffening, make assembly easier and improve the performance of sealing solutions. For example, a common cause of gasket failure is overcompression that deforms and negatively impacts the ability of a gasket to seal effectively. An overmolded gasket that contains a compression stop effectively limits the amount of deflection that occurs when force or pressure is applied, thereby insuring optimal performance of the gasket.
Insert molding can also be used to stiffen a floppy silicone gasket that is difficult for assembly technicians to handle. The use of an insert can provide the right balance between stiffness and flexibility. Increasing the stiffness of a silicone gasket also benefits ruggedization, such as with metal cases and covers, and limits distortion under high pressure.
Insert molded components can have improved gasket sealing performance and longevity relative to the same gaskets not having an insert. Applications with large pressure differentials can unintentionally force or extrude the compound through gaps, destroying the seal resulting in gasket failure. Stiff insert components incorporated into the gasket design help reduce the likelihood of extrusion happening.
Medical and Aerospace Gaskets and Gasket Materials
Insert molded gaskets and seals are beneficial and can have a place in almost any industry or application. The medical industry and aerospace and defense are especially good candidates for insert molding as their critical design parameters and high cost of failure support the nominal additional cost associated with insert molded solutions. Applications to consider are medical gaskets for diagnostic equipment, for aircraft interiors, screen displays or access panels/doors on military vehicles and equipment.
Stockwell Elastomerics has the expertise to insert mold USP Class VI silicones for medical gaskets and the use of various specification grade materials for defense and aerospace applications. These include AMS and A-A-59588 silicones, MIL-DTL-25988 fluorosilicones, and UL 94 flame rated gasket materials.
Contact Stockwell Elastomerics for Insert Molding
Contact Us for further assistance with insert molding, overmolding and co-molding.