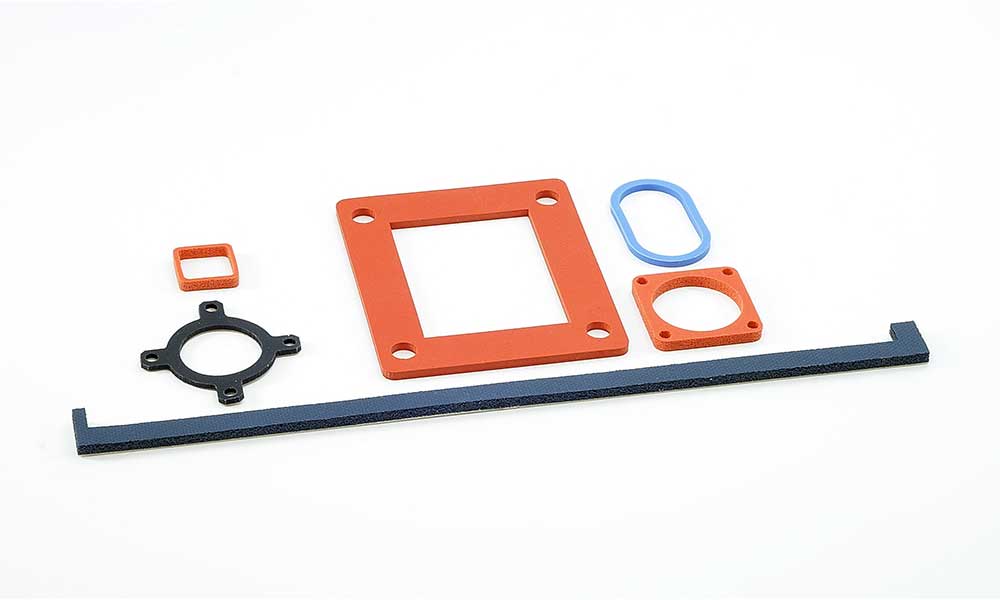
Stockwell Elastomerics manufactures custom high temp gaskets from various high temperature gasket materials to specification.
“High temperature” is a relative term as it pertains to gaskets and seals. Metallic and composite seals can withstand temperatures well above 1000°F. Elastomeric or rubber gaskets on the other hand have much lower operating temperature; an operating temperature above 350°F (177°C) is considered high temperature for polymers. High heat gasket and heat resistant gasket are other names for a high temperature gasket.
Why High Temp Gasket Material?
Environmental conditions should be considered when designing an elastomeric gasket or cushioning pad. Excessive heat will gradually degrade rubber materials as well as deteriorate performance. As a precursor to many rubber tests, heat aging of the rubber material prior to mechanical testing is typical; ASTM D 573, ASTM D 1056, UL 50, UL 48, UL 508, and UL 157 have heat aging requirements. Gaskets and pads exposed to high temperature or prolonged heat exposure can exhibit premature failure leading to water ingress.
Heat Aging Examples
Specification | Test Criteria | Conditions |
---|---|---|
ASTM D 1056 | Compression Deflection | 168 hrs @ 158°F (70°C) / 22 hrs @ 302°F (150°C) |
ASTM D 1056 | Compression Set | 22 hrs @ 158°F (70°C) / 22 hrs @ 212°F (100°C) |
UL 48 (signs) | Tensile or elongation | 70 hours @ 212°F (100°C) |
UL 48 (signs) | Visual (cracking after flexing) | 70hrs @ 212°F (100°C) |
UL 50 (enclosures) | Tensile and elongation | 168 hours @ 158°F (70°C) |
UL 157 (gasket and seals) | Tensile and elongation | 70 hours @ 212°F (100°C) |
UL 508 (industrial controls) | Tensile and elongation | 70 hours @ 212°F (100°C) |
Heat Survival vs. Functionality – Heat Influence on Rubber
Surviving a heat aging test only tells part of the story. Many of the heat aging tests look at tensile and elongation as indicators of permanent deformation, they are indicators of how the polymer is influenced by high temperatures. While some materials will pass the heat aging tests, a significant number of materials will not perform as well in applications due to the duration of heat exposure. Often long term exposure to elevated temperatures that are not as hot as testing temperatures will cause materials to take a compression set or relax. Stress relaxation describes how “push back” of the gasket is reduced. This push back is critical to seal out rain and pressure washing.
Important: When comparing compression set properties take note of the test temperature. Many organic rubber materials are tested at ambient (73°F), and most of these will take a permanent set at elevated temperatures.
Commercially Available High Temp Gasket Materials
The high temperature limit for most commercially available “rubber” products is below 500°F (204 – 260°C); silicone rubber inherently has the best temperature stability of these. The standard operating temperature for silicone ranges from 400 – 500°F (204 – 260°C) with intermittent temperature up to 600°F (333°C). Other materials such as fluorocarbon, EPDM and fluorosilicone have good to excellent heat resistance. This means the gasket material maintains its mechanical properties and will continue to perform as designed without reversion.
General Operating Temperatures for Common Rubber Materials*
- Urethane: less than 250°F (121°C)
- Natural Rubber: less than 250°F (121°C)
- Chloroprene (Neoprene): less than 300°F (149°C)
- Nitrile (Buna-N): less than 300°F (149°C)
- EPDM: less than 400°F (204°C)
- Fluorosilicone: 400 – 500°F (204 – 260°C)
- Fluorocarbon: 400 – 500°F (204 – 260°C)
- Silicone: 400 – 500°F (204 – 260°C)
* Temperatures are general; values will vary with grade. Refer to specifications for actual product temperature ratings.
Silicone, fluorocarbon, and fluorosilicone and EPDM are considered high temperature rubber materials and are readily available in sheet stock form (solid silicone sheet, closed cell sponge, and open cell foam). Silicone may also be injection molded or compression molded in various hardnesses, from as low as 10 durometer to 80 durometer on the Shore “A” scale. If very low temperatures are required, silicone or fluorosilicone would be the best choice. Fluorocarbon and fluorosilicone are generally readily available. However, these materials are rather costly specialty products used where chemicals and fuels are present.
Contact Stockwell Elastomerics for High Temperature Gaskets and High Temp Gasket Material
Contact Us for further assistance with custom high temp gaskets, high heat gaskets, heat resistant gaskets, and high temperature gasket material.