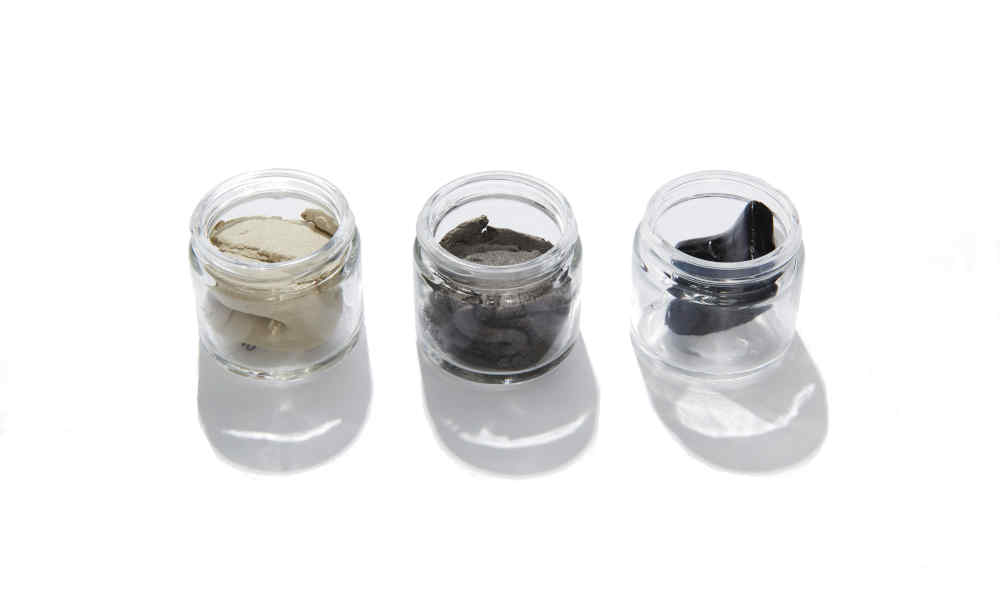
Custom formulated silicones are designed to meet specific requirements that can provide specific material or performance properties such as enhanced compression set, greater elongation, higher surface energy, a lower coefficient of friction, or electrical or thermal conductivity. Silicones are versatile elastomers, but it takes a network of experienced silicone chemists to develop custom formulations like this.
Stockwell Elastomerics has partnered with leading silicone suppliers that have deep knowledge of silicone chemistry and can evaluate customer requirements to determine to best approach. At a time when some suppliers are more interested in reformulating existing products, Stockwell Elastomerics’ knowledge of particular suppliers with an interest in taking on custom projects is an important differentiator. These relationships, and access to technical staff, can be leveraged for custom projects. Stockwell Elastomerics also supplies custom SKUs and custom composites if needed.
Solving Unique Challenges
Stockwell Elastomerics’ in-house material knowledge combined with its network of expert material and process partners have solved unique challenges using custom silicone formulations. Examples include flame retardant LSR that meets UL 94V-0 requirements and is also electrically dissipative. Stockwell Elastomerics has an in-house material testing laboratory, and its AS9100 / ISO 9001:2015 certification demonstrates its commitment to quality control (QC) and quality assurance (QA).
Base Polymers
Silicones are derived mainly from silicon, oxygen, carbon, and hydrogen atoms; however, not all silicone elastomers are the same. Along with additives, fillers, cross-linking agents, and catalysts, the base polymer influences the properties of the final product in terms of material and performance characteristics. With the knowledge of the customer applications, formulating partners can combine the right ingredients in the right amounts for custom developed solutions.
Silicone chemistries include:
- Methyl-based silicone (dimethyl silicone) provides thermal stability, low surface tension, chemical inertness, low toxicity and odor, and electrical insulation.
- Phenyl-based silicone (diphenyl silicone) resists higher temperatures than dimethyl silicone and offers increased aromaticity. It also has a higher refractive index and a lower glass transition temperature than methyl-based silicone.
- Fluoro-based silicone (fluorosilicone) incorporates fluorine atoms for enhanced chemical resistance, greater high-temperature resistance, and stability over a wider temperature range. Fluorosilicone also has excellent fuel and oil resistance and low gas permeability.
Additives and Fillers
Custom formulated silicones and fluorosilicones may include various additives and fillers to modify material and performance properties. For example, reinforcing agents such as silica or glass fibers can be added to enhance strength, or additives to improve lubricity. Flame retardants that meet UL 94 standards, pigments for color, plasticizers for flexibility, and UV stabilizers for resistance to sunlight can also be added to base polymers. The selection and concentration of additives are determined by the desired compound characteristics.
Cross-Linking and Catalysts
Like standard silicones, custom silicone formulations need to be cross-linked to form a solid material. Common cross-linking methods for silicones include heat curing, catalyst additions, and condensation curing which uses moisture in the air. Catalyst additions include peroxide curing and platinum curing. Platinum cured silicones have stronger physical properties and lower shrinkage values than peroxide-cured silicones. In addition, platinum cured silicones have lower levels of off gassing.
Processing, Testing, and Optimization
Custom formulated silicones can be processed as liquid silicone rubber (LSR), high-consistency rubber (HCR), or room temperature vulcanizing (RTV) silicone. Before production begins, however, custom silicone formulations undergo mechanical, thermal, and chemical tests. They may also undergo an iterative optimization process where adjustments are made to composition and processing parameters until the specified performance characteristics are achieved.
Custom SKUs
In addition to custom formulated silicones, Stockwell Elastomerics supplies custom fabricated combinations of solid, foam, and sponge silicones. Many of these silicones that are distributed and fabricated are stock materials from leading manufacturers such as Rogers Corporation and Saint-Gobain. If an application needs a custom product (color, surface texture, performance), please contact Stockwell Elastomerics to discuss options and approaches.
Custom Composites
Stockwell Elastomerics can also laminate different materials together to provide custom composites. These sandwich-like structures leverage the material and performance properties of the constituent layers and support die cutting and waterjet cutting. Custom composites can also come with an adhesive backing for ease of installation.
Contact Stockwell Elastomerics for Custom Formulated Silicone
Contact Us for further assistance with custom formulated silicones and fluorosilicones for fabrication or distribution.