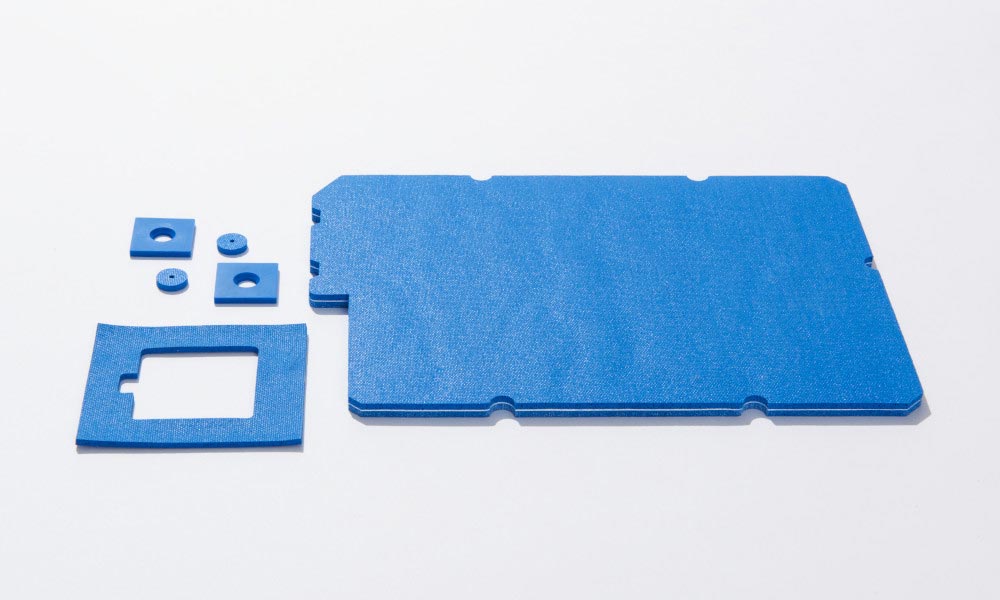
Stockwell Elastomerics manufactures chemically resistant gaskets using a variety of gasket materials to address compatibility concerns in high tech industries. Engineers require robust gasket solutions for applications in harsher environments.
Stockwell Elastomerics’ Applications Engineers can help eliminate time spent fishing through publications and resources to find the correct chemically resistant gasket material. Stockwell Elastomerics has a variety of resources and industry expert partnerships to get answers on tough chemical compatibility issues. Once a material is selected, Stockwell Elastomerics offers rapid turn samples to help customers iterate through designs and validate material and design choices. When designs are finalized, Stockwell Elastomerics can support production through waterjet cutting, die cutting, molding, or other custom gasket fabrication methods.
What are Chemical Resistant Gasket Materials?
Gasket materials have different levels of chemical resistance, which is the ability to maintain their original properties after exposure to specific chemicals in particular environments. During chemical resistance testing, samples of gasket materials are immersed in various test fluids under different time and temperature conditions. These chemicals and conditions are typically described in test standards through ASTM specifications, but industry-specific and customer-specific test conditions may also exist. Stockwell Elastomerics has access to a variety of industry experts and literature to help customers determine the ideal fit for specific chemical resistant gaskets.
Typically, chemical resistant gasket materials are measured by changes in physical properties (weight, volume, dimensions) or mechanical properties (tensile strength, impact strength, elongation) after a specified immersion time and temperature. The table below describes these materials along with other commonly used rubber compounds. The bolded items in the chart below are some of the high performance materials used by Stockwell Elastomerics that have superior chemical resistance.
General Chemical Resistance
Material Common Name | Resistant To: | Attacked By: |
---|---|---|
Neoprene | Moderate chemicals and acids, ozone, oils, fats, greases, many oils, solvents | Strong oxidizing acids, esters, ketones, chlorinated, aromatic and nitro hydrocarbons |
EPDM | Animal and vegetable oils, ozone, strong and oxidizing chemicals | Mineral oils and solvents, aromatic hydrocarbons |
Buna-N | Many hydrocarbons, fats, oils, greases, hydraulic fluids, chemicals | Ozone (except PVC blends), ketones, esters, aldehydes, chlorinated and nitro hydrocarbons |
Silicone | Moderate or oxidizing chemicals, ozone, concentrated sodium hydroxide | Many solvents, oils, concentrated acids, dilute sodium hydroxide |
Styrene-butadiene rubber (SBR) | Most moderate chemicals (wet or dry), organic acids, alcohols, ketones, aldehydes | Ozone, strong acids, fats, oils, greases, and most hydrocarbons |
Fluorosilicone | Moderate or oxidizing chemicals, ozone, aromatic chlorinated solvents, bases | Brake fluids, hydrazine, ketones |
Viton® | All aliphatic, aromatic, and halogenated hydrocarbons, acids, animal and vegetable oils | Ketones, low molecular weight esters and nitro-containing compounds |
Chemical resistance testing is typically quantified in a tiered rating system to show varying levels of chemical interaction. For example, consider an application that may interact with jet fuel (JP-10). In consulting a chemical resistance testing resource, the results are as follows:
Tested Chemical | Elastomer | Result |
---|---|---|
Jet Fuel, JP-10 | Silicone | NR at 70 °F * |
Jet Fuel, JP-10 | Fluorosilicone | A to 70 °F ** |
* >50% volume increase or > 60% tensile strength loss at 100% concentration, or concentrated, or saturated solution at 70 °F. Severe attack | ||
** <15% volume increase or <15% tensile strength loss at 100% concentration or concentrated or saturated solution, to 70 °F. Little or no chemical attack |
(Source: Chemical Resistance Guide to Elastomers III, Kenneth M. Pruett, Compass Publications)
As shown above, volume increase and tensile strength changes help describe the chemical resistance. JP-10 has a very severe interaction with silicone, and it is likely that material would fail in use. However, fluorosilicone has little to no reaction, as volume and tensile strength change minimally. This is why fluorosilicone is a great chemical resistant gasket material in the aerospace industry.
Silicone, fluorosilicone, and Viton® are often chosen as chemical resistant gasket materials due to the benefits outlined in the tables above. Customers in the technology sector often require robust chemical resistance: For example, medical device gaskets need resistance to cleaning agents, just as defense system gaskets require resistance to jet fuels. The chemical resistance of these materials helps ensure a robust and longterm sealing solution, especially when combined with the superior mechanical properties and temperature resistance each of the materials offer
Contact Stockwell Elastomerics for Chemical Resistant Gaskets
Contact Us for further assistance with custom gaskets for applications requiring chemically resistant gasket materials.
Viton™ is a trademark of The Chemours Company FC, LLC.